APPROACH
Commercially available fossil-based and bio-based PE are sourced, altered, and compounded to suit melt spinning and downstream processes. Melt spinning (POY) processes are developed using those compounds, with iterative adjustments to the compounding as needed. A false-twist texturing (DTY) process is developed using the as-spun yarns, with necessary modifications to ensure the POY quality required for DTY production. Using the textured yarns, a seamless knit process is created, refining the DTY process as needed. A demonstrator shirt is produced from the knitted textiles, with bio-based finishing applied to meet required properties. The project considers a design for recycling approach. After the project’s success, TECNARO will supply granulate and masterbatch to filament producers, BBE will market the modified machines and processes, and FALKE will market the textile demonstrators. HOFFMANN + VOSS validate the recyclability of the single-origin textiles in subsequent projects. ITA will incorporate the project results into further scientific research.
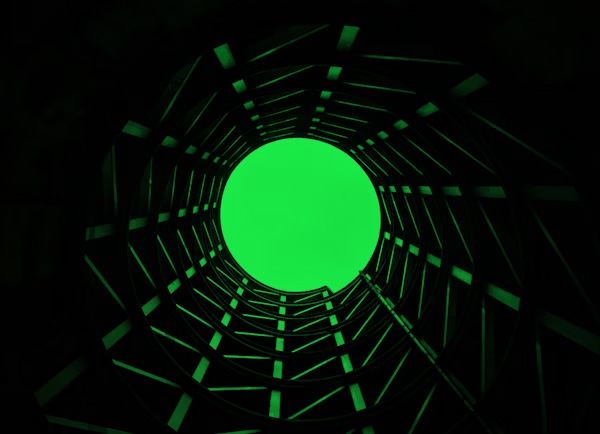