APPROACH
The project structure consists of four development steps with increasing complexity. The four steps are supercritical drying, finishing, assembly & testing, and integration. The project starts with the optimization of the aerogel nonwoven drying process at ITA. In the second step, the aerogel nonwoven undergoes post-treatment. The finished aerogel nonwovens will then be assembled to test specimens and tested at Adidas. The fourth step is to integrate aerogel nonwoven into different cold-weather garments. All four development steps will be supported by continuous accompanying assessments from the TransitionLab. The material acceptance, desired characteristics, and later product acceptance will be investigated. For the LIGHT LINING project at least 3 iteration steps are planned. To ensure the necessary information flow for a steady improvement and adjustment of the materials an agile project management approach is chosen. Each iteration step will uncover new requirements for the materials which then can be directly applied to improve the product. Following the last iteration, the aerogel nonwovens will be integrated into state-of-the-art cold insulation clothing and tested.
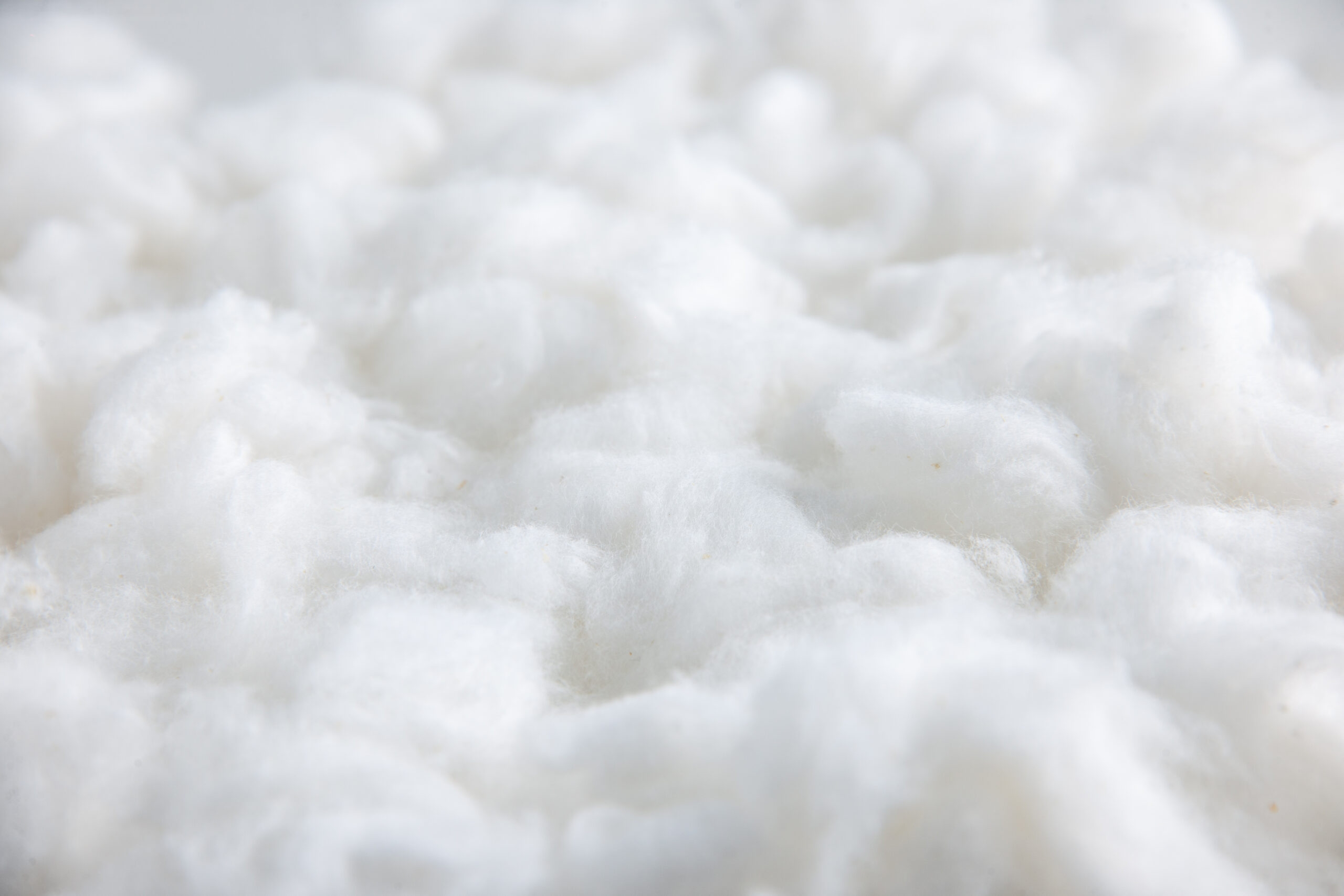